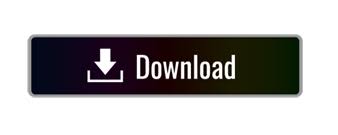
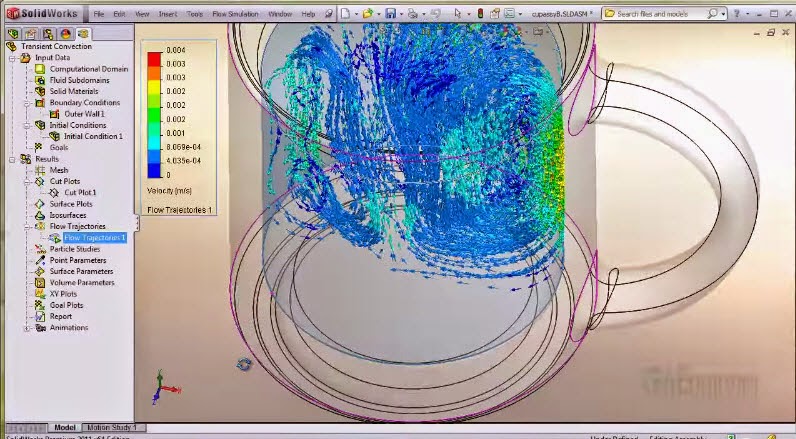
Define the End time of your simulation.The time control settings are very important in transient convective heat transfer simulations. Figure 9: Assignment of volumetric heat sources. The table assignment is just as explained in the transient heat transfer article. In a transient analysis, you can define the heat generation as time-dependent. You can use this boundary condition to define the volumetric heat generation. Figure 8: Add convective heat transfer coefficient together with conductive wall thickness. In addition, you can use the empirical approximations or visit this website to approximate the convective heat transfer coefficient. Check out this article to learn more about the thermal wall conditions. If the thermal conductivity within the casing is also an important parameter, you can use the wall boundary condition to assign convective heat transfer effects and thickness of the casing material. Figure 8: Add heat sources on surface elements. You can use a wall boundary condition to define the heat dissipation from the the component surfaces.
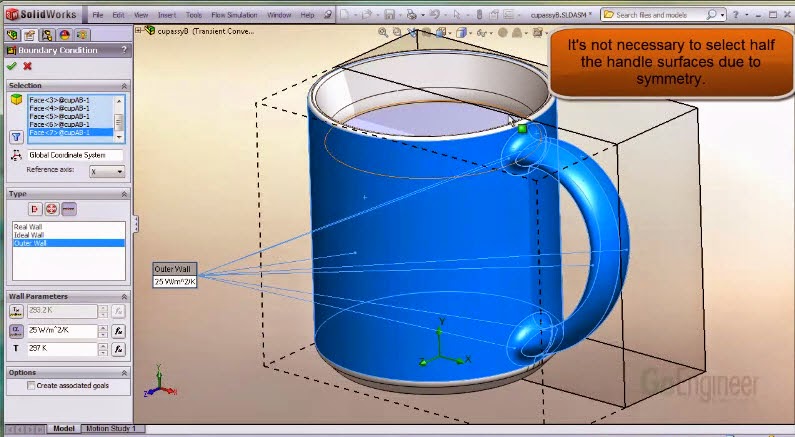
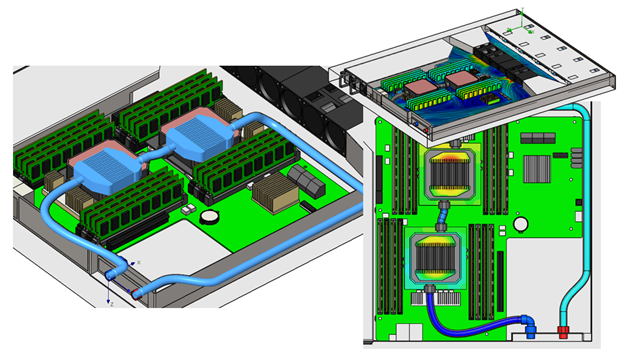
#Solidworks flow simulation transient natural convection how to#
Check out the thermal management tutorial to see how to assign a fan curve. You can use custom boundary conditions to assign an inlet or outlet fan. If you expect the natural convection effects to dominate the flow at the inlet and outlet, use Natural Convection Inlet/Outlet Boundary Condition. In this article, you will learn about the commonly used boundary conditions for transient heat transfer analysis. You can find the available boundary conditions for heat transfer analysis on this page. Figure 7: Defining initial temperature of the fluid domain. Moreover, you can create a subdomain to define the initial temperatures in specific regions. To clarify, the Temperature section is a quick way to assign temperature values on the whole fluid region. Initial Conditionsĭefine the initial temperature of the fluid domain. In addition, you can check this knowledge base article to see how to create custom materials. For the others, you can use the default materials as guidance to apply the properties of the fluid you are planning to use.įor more information about the thermal properties, check the documentation page. You can use SimScale’s default material library for common materials. Material Assignmentĭepending on the compressibility assignment in the simulation setup, expected material properties vary. Gravity should be defined with respect to global coordinate system. These details will increase simulation time and costs.įigure 5: Simulation setup of a transient convective heat transfer analysis. Depending on the complexity you want to reach, you can include compressibility or radiation effects too.If you precisely need to see the conditions within a specific time limit, then select Transient time dependency. As an example, if you would like to see the maximum or minimum temperature the system will reach under stable conditions, choose steady-state. First, ask yourself whether your problem requires a time-dependent analysis or not. Transient simulations are computationally expensive.In addition, if you need to know more information regarding the CAD preparation, visit this page. This is not a must, but highly recommended for the solver stability. If forced convection takes place, extrude the inlets and outlets (usually 3-5 times the hydraulic diameter of the channel). No matter what you are analyzing, do the following: Electronics equipment is often designed with a casing. We need to create the fluid domain and get rid of the solid parts. CAD PreparationĬonvective heat transfer analysis examines the fluid. Figure 3: Define a minimum edge size and clean the details below this tolerance. Having a standard minimum thickness will later help you in the meshing stage. (small nuts, bolts, pins, etc.).Įvery detail has an influence on the performance, but ask the following question to yourself: Does this detail have a significant impact on the results? Figure 2: Common CAD cleaning measures on PCBs.įinally, choose a minimum size and adjust the small edges to this specific size. In other words, remove extra or unnecessary features/components. This article explains how to find faults. Secondly, avoid overlapping solids (unless they represent cell zones).The CAD model should only consist of solid parts. Firstly, avoid sheet/surface elements.Figure 1: Temperature distribution on a Printed Circuit Board (PCB).
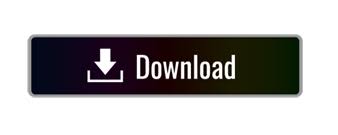